智能制造之个人解读
再说一个例子,假定全国每年对某企业需要的某型医疗设备是2000台,那么在不开拓新的市场前提下,假设这个企业不断应用精益和技术来整制造升级,能省下的部分成本有哪些?细想来无非是一个无价值增值时间缩短所带来的人力成本的节约和价值增值过程中能源消耗成本的减少,而对于一个生产成熟的企业来说,这些成本很多时候都是以BaseCost的形式固定下来,那么省来省去省了个啥,无非就是个电费。对于这样情形要搞智能制造,要么需要企业拓展市场从2000台拓展到3000台,要么要开拓新的产品市场。在不满足企业的市场扩大的前提下,搞智能制造的收益基本就是看不出来的。因而笔者认为智能制造最先要看的就是业务层面的事情,必须在外部市场要求企业工厂满荷甚至超负荷运转的前提下才有可能应用智能制造相关技术实现缩减成本增加利润的目标。其次很多成熟产品的生产和市场占有都是符合S曲线规律的,在效率提升到某个奇点后,每提升一个点生产效率或市场占有率所付出的成本都是巨大的,这时候用智能制造实现这样的目标只怕投入产出比都是没有了。类似的例子还有很多,比如很多日本企业在过去10年就毁在了提升这S曲线的最后一段上。
再看看第二个层面,假定一家工厂现在满足从业务角度绝对有市场的这个条件,而且工厂也满负荷甚至超负荷运转了。这时候整智能制造,就该从精益下手了。具体来说就是该从清晰化生产流程开始,即明确每个人的权责和该做的事情;他的上游是谁,该交付给他哪些交付物以协助他完成他的工作;他的下游是谁,他该交付哪些交付物给下游方便下游进行工作。这样一件事可以用一张泳道图来描述,可以说这是精益的第一步。根据这张泳道图,现在需要细化的是每个人自身的工作流程,一张流程图描述清楚他个人所做的工作。至此,算是流程清晰化了。接下来就是发扬日本人的精益精神,先鉴别每个人自身工作哪些是有价值增值的,哪些是无价值增值的。一个简单的判断原则,如果一个人的无价值增值时间与有价值增值时间之比大于等于1,那么就该充分发挥精益精神革这个小朋友的命了。好不容易省下的个人无价值增值千万不能因为流程不顺又在整个流程里给浪费了。这里举个例子啊,比如某小朋友经过精益改造,总算把无价值增值时间缩短到原来的60%,如果预估算从4小时变到现在的2.4小时,省下了1.6小时。但是如果在他与下游交接不顺或者某些情况发生的时候又把这1.6小时给浪费了,那就真是白辛苦了,泥牛入海啊!因而可以看出流程清晰有多重要了吧!至于其他的精益工具5S啊,JIT啊都可以用,但是流程清晰必须先行。笔者经历过很多精益是流程都没弄清就整5S,Kanban,TPM,VSM,这真的很让人无语。这个层面智能制造的目标就是从每个人层面最小化无价值增值时间,从流程层面就是砍掉不需要的冗余的环节。更坦白的说就是剥削人更彻底点和裁撤多余的人头,这两件事无论哪件都是触动利益链的事,能不能干先自己掂量下。
笔者认为只有上面两个层面的事情全部做的差不多了,才该是应用技术去兑现智能制造的目标的时候。应用技术来解决基本都是某个点的问题,很多时候是为了提升价值增值劳动的效率的,需要支付相当成本才可能让技术兑现目标。也正是由于做好了上面两个层面,制造技术上带来的成效才能直观的反应在流程中的时间节约上。举个例子,由于更换新的智能相机检测零件质量相比过去目视检查时间缩短了80%,那么一样的辛苦缩短下来的80%时间千万需要在流程中体现出来,别让它泥流入海了。至于具体的技术帮助实现智能制造,不在这展开了,太多了没法枚举。
个人解读的局限性
最后谈谈个人解读的局限性,主要个人思考的出发点还是在企业内部运行上,因而很多时候会有很多不足。比如从第一个层面的供应链和业务去看,如果本企业处于采购强势地位,那么还有种最简单的兑现智能制造的优化目标的办法,压供应商,但是这是种Win-Lose的业务模式。再比如,在整个行业链是上该怎样实现智能制造,这个问题也没能思考和实践,更甚一层跨行业的合作该如何实现智能制造。视野有限,也就只能摆出问题,欢迎大家的探讨。
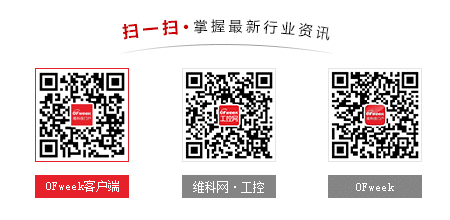
图片新闻
最新活动更多
-
5月8-10日立即报名>> 国际物流解决方案展览会
-
5月16日火热报名>>> OFweek锂电/半导体行业数字化转型在线研讨会
-
5月22日火热报名中 >> 瓦楞行业张力控制解决方案在线研讨会
-
5月31日立即报名>> 【线下论坛】新唐科技2024未来创新峰会
-
8月27-29日马上报名>>> 2024(第五届)全球数字经济产业大会暨展览会
-
8月27-29日火热报名>>> 全数会2024中国深圳智能制造与机器人展览会
推荐专题
发表评论
请输入评论内容...
请输入评论/评论长度6~500个字
暂无评论
暂无评论