技术文章:HIC失效模式和失效机理
3.厚膜电阻失效
厚膜电阻器的主要失效模式为参数漂移和参数不稳定,其失效机理及原因包括:
(1)Pd-Ag电阻器在湿热环境下由于化学成分的变化导致其阻值不稳定,阻值增加的原因与Pd、Ag元素被氧化有关,阻值减少的原因与Ag被还原有关。
(2)Pd-Ag电阻器直接暴露于氢气中参数不稳定,在工艺过程中封装材料环氧树脂、黏合剂、焊剂可能释放氢气,若厚膜电阻表面保护层玻璃釉不良,则会触及氢气,导致参数发生变化。
(3)厚膜电阻在界面应力作用下导致开裂,应力来源于电阻膜与其保护玻璃釉膜界面之间的应力失配或灌封电路树脂固封时热胀冷缩对电阻膜产生的机械应力。
(4)激光调阻引入的缺陷,造成阻值不稳定。
(5)高压脉冲使用情况下,厚膜电阻产生很大的阻值变化,一方面原因是厚膜中导体金属与玻璃之间、导体金属颗粒之间存在不完全浸润,另一方面原因是高压脉冲击穿局部膜层中的玻璃相引起电阻等效网络的阻值变化。
4.薄膜基板及互连失效
薄膜导体的主要失效模式是开路和导体之间短路,其失效机理及原因包括:
(1)电化学腐蚀,薄膜金属与环境介质带来的其他离子发生化学反应形成金属化合物,损坏薄膜金属的完整性。
(2)薄膜金属发生电迁移导致布线烧毁,由于电迁移效应将使金属阳极附近出现迁移原子堆集,而在金属阴极附近形成空隙,造成薄膜金属的严重破坏、局部电流密度增大,甚至过热烧毁。
(3)Cr/Cu/Au薄膜导体与Pb-Sn焊料结合后,存在污染和出现水汽的条件,会出现明显Pd-Ag枝晶状迁移物或大面积的Cu迁移物,元素迁移与C、O、Cl、S沾污元素有关,也与相邻导体间电位差有关。
(4)薄膜电容器的ESD损伤,相同工作电压下薄膜电容容量小的比容量大的对ESD更敏感;而相同容量的薄膜电容器工作电压高的比工作电压低的对ESD更敏感;薄膜电路ESD测试中,薄膜电容器的ESD最为敏感。
(5)SiO2薄膜电容器失效,薄膜电容器下电极边缘“台阶”处电场畸变,且“台阶”处电介质膜层较薄,容易在“台阶”处发生介质击穿,导致电容短路。
三、厚膜、薄膜基板与元器件的焊接/黏结失效
1.厚膜基板与元器件的焊接失效[4]
混合集成电路内装元器件与厚膜基板的焊接,是实现电路功能的重要互连部位。与厚膜基板焊接的元器件主要有片式元件和半导体芯片。焊接结构的主要失效模式有元器件脱落、片式元件/芯片开裂和因焊接缺陷导致的散热不良。失效机理及原因包括:
(1)Pb-Sn焊组装中,含金类厚膜导体溶解在焊料中容易形成Au-Pb-Sn金属间化合物,有可能使基板与元器件的焊接互连强度下降。
(2)厚膜基板氧化或烧结不当引起表面玻璃釉堆集,造成厚膜基板可焊性不良,元器件焊接强度下降。
(3)Pb-Sn焊料、Au-Pt-Pd厚膜基板结构,焊料与厚膜基板间会形成金属间化合物(IMC)AuSn4、PtSn、PdSn,若长期工作在高温条件下,较为脆性的IMC层将继续生长加厚,导致芯片抗温度循环能力下降,甚至开裂。
(4)表贴片式电容器端电极开裂,典型的片式电容器有三种端电极结构:Ag、Pd-Ag、Pd-Ag/Ni/Pb-Sn,若端电极焊点为凸状外形,则焊点边缘应力高度集中,温度冲击下电容由端头破裂延伸至瓷体内部而开裂。
(5)功率芯片烧结缺陷导致热击穿烧毁,其原因包括芯片烧结面积不足、存在空洞,影响了芯片焊接强度,在高温应力作用下,空洞缺陷引起焊接界面裂纹、热阻增加,导致功率芯片热性能退化、焊接强度下降;另外,芯片背面金属化可烧结性差,难以形成良好的欧姆接触,如衬底Cr-Ni-Au的芯片背面Ni阻挡层和Au层结构的设计不合理,是影响芯片Si材料与焊料Au互扩散和共熔的主要因素,不能形成良好的AuSi共晶焊接层。
2.薄膜基板与元器件的焊接失效
传统的薄膜基板采用Ni-Cr/Au金属化膜,若采用锡焊工艺,当温度控制稍高或时间稍长时,薄膜表层金镀层极易溶于焊锡,并暴露出与锡不浸润的Ni-Cr层从而导致焊接失效。即使焊接好的基板也会在高温使用过程中,因Au-Sn继续互溶而使可靠性降低。改进方法是在Ni-Cr/Au金属化膜的基础上镀Ni/Sn-Bi、Ni-Cr/Au/Ni/Sn-Bi多层结构,化学镀Ni层作为焊接的中间阻挡层,表面金属Sn-Bi合金电镀层作为焊接层。
3.厚膜基板与元器件的黏结失效
厚膜基板与元器件的黏结采用两种功能的有机胶:固定用有机胶、导电用有机胶。主要失效模式为由元器件脱落、开裂和黏结材料老化引起的芯片电参数漂移。失效机理及原因包括:
(1)采用环氧银导电胶黏结小功率芯片,经125℃/1000h老化后,常表现的失效模式是芯片脱落或晶体管芯片的饱和压降VCES增大,主要原因是配方不当,导电胶偏少,致使黏结的物理机械性能差;烘干固化速度太快,氧化银未充分还原,聚合树脂未能很好固化反应;封装内部的有害残余气体在高温下使导电胶加速老化,导致接触电阻增大。
(2)在高温贮存条件下,导电胶的黏结强度随时间而降低,导电胶中黏合剂的热老化是导致导电胶黏结强度降低的主要原因。
四、键合互连失效
混合集成电路的内引线键合主要有双金属键合和单一金属键合两种形式,其失效模式为键合拉力下降和键合点脱开。键合失效在混合集成电路失效中占比23%,其失效类型及机理有:
(1)Au/Al键合界面退化,铝丝与厚膜金导体键合,在高温条件下Au/Al键合界面发生严重退化,导致键合拉力下降。
(2)Au/Cu键合界面退化,铜丝与镀金引线框架键合或者金丝与铜引线框架键合,在200~300℃温度下,界面形成柔韧的金属间化合物Cu3Au、AuCu和Au3Cu[5],界面出现Kirkendall空洞,长时间后导致键合强度下降。
(3)Cu/Al键合界面退化,铜丝与芯片铝键合,在100~500℃温度下,界面通过相互扩散生成金属间化合物CuA12、CuAl、Cu9A14,但不会生成Kirkendall空洞,由于CuA12的脆性,导致剪切强度明显下降,并且铜丝还存在容易氧化的问题。
(4)Al/Ag键合界面退化,铝丝与镀银引线框架键合,一般温度下,Al/Ag键合相互扩散和退化明显,易生成多种复杂金相结构;在175℃以上,若不使用Al/Ag键合,容易因金属间化合物加速生长而生成Kirkendall空洞,同时银表面极易被氧化。
五、布线基板与外壳焊接失效
布线基板与外壳焊接的失效模式主要是附着强度下降,其失效机理及原因有:
(1)由于基板焊接结构设计和工艺控制不当,引起焊接浸析导致基板附着力下降,原因是基板背面金属化层过薄、焊接温度过高、再流焊次数过多。
(2)因焊料选择不当,影响了基板焊接的附着强度和长期可靠性,原因是在基板与镀Au外壳间的焊接中使用了含In的焊料(Pb-In)。
六、功率器件过热失效
当器件的工作温度超出规定的结温上限时,出现器件失效或参数超差,称为过热失效,典型电子元器件的最高允许结温TJM和额定功率壳温上限(额定功率下的最高允许温度)TS/TN见表3。因此必须保证元器件工作在最高允许结温TJM和额定功率壳温TS/TN以下,这是功率元器件过热控制设计的基本原则。可通过选择适当的黏结材料、基板、外壳控制散热带来的问题。
器件芯片的最高允许结温为TJM,对于硅芯片TJM=175℃,对于锗芯片TJM=80。一旦器件芯片的结温超过TJM,则芯片会出现参数漂移甚至烧毁。在器件功率和外壳温度一定的情况下,影响器件结温的主要因素是封装热阻,主要表现在三个方面:热流路径上的封装结构尺寸、封装材料的热传导系数和热流路径上的焊接/黏结界面热阻。
表3 典型电子元器件的最高允许结温TJM和额定功率壳温上限TS/TN
七、气密封装失效
气密性封装按材料可分为金属气密性封装和陶瓷金属气密性封装两种形式。气密性封装的失效模式为水汽超标,即水汽含量超过了标准要求(GJB 548规定水汽含量<5000×10^-6)。气密性封装内部水汽超标的来源一般有三个:腔体内各部分材料表面和内部吸附的水汽随温度变化而解吸;封盖操作时封口气氛中的水汽;外壳漏气部位渗入水汽。
混合集成电路在老化后内部水汽超标导致漏电增加。研究发现封装后的混合集成电路经125℃老化试验后,助焊剂热退化会产生超量的水汽,除了水汽外,气体分析还检测出二氧化碳、异丙醇、甲醇。漏电流是基板表面带有残余助焊剂的布线导体之间出现金属迁移的结果。
气密性封装中常采用低熔玻璃进行陶瓷熔封封装,由于陶瓷材料在使用前呈粉末状,表面积很大,因此难免在加工中吸收一些潮气,尽管这些水分在封接前可以通过加热将其排除,但并不能彻底排除干净,容易在封接后残留在封装的空腔中,对芯片和其他部位造成腐蚀。
外引脚玻璃绝缘子破裂导致气密性封装失效。封接材料间的热膨胀系数差异是影响封接质量的关键;玻璃绝缘子中存在气泡,在热应力作用下,气泡处产生的应力集中导致裂纹萌生和迅速扩展;金属环、引脚玻璃封接界面缺少必要的晶间氧化层过渡或氧化层很薄,不能形成封接界面材料的相互浸润,降低了玻璃绝缘子的密封性和密封强度。可参考国外绝缘子结构,选用铁镍合金与铜封接,再选择膨胀系数较高的软玻璃,使中间引线与基座间形成分级封接,以降低封接应力,提高产品的封接质量。
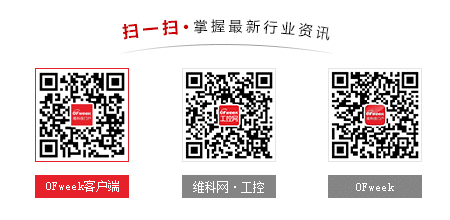
图片新闻
最新活动更多
-
7月3日立即报名>> 【在线会议】英飞凌新一代智能照明方案赋能绿色建筑与工业互联
-
7月22-29日立即报名>> 【线下论坛】第三届安富利汽车生态圈峰会
-
7.30-8.1火热报名中>> 全数会2025(第六届)机器人及智能工厂展
-
7月30-31日报名参会>>> 全数会2025中国激光产业高质量发展峰会
-
即日-2025.8.1立即下载>> 《2024智能制造产业高端化、智能化、绿色化发展蓝皮书》
-
精彩回顾立即查看>> 【在线会议】Solution Talks |Computex 2025关键趋势深读
推荐专题
- 1 数智破局·生态共生:重构全球制造新引擎 2025 WOD制造业数字化博览会即将在沪盛大启幕
- 2 【重磅来袭】6月17日上海见!全球智造巨头聚首,60余场前沿论坛,制造业数字化盛会邀您共启数智破局之旅!
- 3 安森美正式参评“维科杯·OFweek 2025中国工业自动化与数字化行业优秀产品奖”
- 4 当数智工业邂逅大湾区,看PHIIDF2025如何破界,链动全球!
- 5 抢先解锁!全数会2025机器人及智能工厂展览会核心亮点速递
- 6 硬核登场!凌科LP-12系列 90°工业级连接器上市,打造行业高可靠连接解决方案
- 7 【最后召集】6月17-19日,60+论坛剧透制造业未来,200+全球巨头携制造业黑科技齐聚,制造业数字化转型巅峰盛会即将启幕!
- 8 4.77 亿募资!年赚 1.11 亿的智能配电 “小巨人” 冲刺创业板,在手订单超 6 亿!
- 9 欧姆龙正式参评“维科杯·OFweek 2025中国工业自动化与数字化行业优秀产品奖”
- 10 世界计量日盛会启幕,聚焦测量体系变革:质量、效率与动力
发表评论
请输入评论内容...
请输入评论/评论长度6~500个字
暂无评论
暂无评论